A magnetic lifter is a tool that uses magnetic force to attract and lift heavy objects. It is widely used in various industrial fields. It is usually made of permanent magnetic materials and attracts metal objects through a strong magnetic field, thus replacing traditional equipment such as hooks, chains or wire ropes.
A magnetic lifter relies on the magnetic force of a permanent magnet to establish a strong magnetic attraction between the target object and the magnetic lifter, so that the object can be lifted safely and efficiently.
Advantages of magnetic lifters
High efficiency:
Magnetic lifters have a fast adsorption speed, which can greatly improve the efficiency of lifting operations and reduce manual operation time.
No power supply required:
Compared with electric lifters, magnetic lifters do not require power or batteries, which greatly reduces maintenance and use costs.
Safety:
The strong magnetic force enables the magnetic lifter to firmly adsorb heavy objects, avoiding the risk of human operation errors or the risk of the hoist slipping, and improving the safety of the operation.
Space saving:
Magnetic lifters are small in size and can be used for lifting operations in limited spaces, especially suitable for small working environments.
Product parameters of magnetic lifters
Model | YC-100 | YC-300 | YC-500 | YC-600 | YC-1000 | YC-2000 | YC-3000 | YC-5000 |
Rated lifting strength (KGF) | 100 | 300 | 500 | 600 | 1000 | 2000 | 3000 | 5000 |
Cylindrical lifting strength (KGF) | 50 | 150 | 250 | 300 | 500 | 1000 | / | / |
Max. pull-off strength (KGF) | 350 | 1050 | 1750 | 2100 | 3500 | 7000 | 10500 | 17500 |
L | 92 | 163 | 216 | 234 | 264 | 370 | 452 | 720 |
B | 62 | 92 | 120 | 122 | 172 | 232 | 274 | 296 |
H | 67 | 93 | 116 | 118 | 168 | 221 | 266 | 266 |
R | 140 | 180 | 220 | 220 | 260 | 450 | 520 | 700 |
Operation temperature(‘C) | <80 | <80 | <80 | <80 | <80 | <80 | <80 | <80 |
Dead weight (Kg) | 3 | 10 | 21 | 24 | 50 | 125 | 220 | 398 |
Lifting capacity (load capacity)
The material of the hoisted object, the surface smoothness and the magnetic strength of the magnetic lifter may affect the lifting capacity.
Adsorption surface size
The larger the size of the adsorption surface, the more evenly the magnetic force can be distributed, thereby improving safety and stability.
Operating temperature range
The common operating temperature range is -20°C to 80°C, and high or low temperature environments may reduce the magnetic force.
Adsorption force retention time
Some high-quality magnetic lifters are designed with a mechanism to resist magnetic force attenuation, which can maintain a strong adsorption force for a long time.
Safety factor of the magnetic lifter
Generally speaking, the safety factor of a magnetic lifter is at least 3:1, that is, the actual load of the lifter cannot exceed one-third of its rated load.
Common user pain points and solutions
Pain point 1: Insufficient suction
Solution: Make sure the magnetic force of the lifter matches the rated load when purchasing. Check the magnetic force of the magnetic lifter regularly to avoid magnetic force decay after long-term use.
Pain point 2: High initial cost
Solution: Although the initial investment of the magnetic lifter is high, in the long run, it can improve work efficiency, reduce labor costs, and reduce accident rates, thereby saving more costs.
Pain point 3: Troublesome maintenance and care
Solution: Keep the magnetic lifter clean and dust-free by regularly cleaning the magnetic surface to avoid iron filings or debris affecting the adsorption effect. At the same time, regularly check the magnetic force and overall condition of the lifter.
Pain point 4: Danger caused by improper use
Solution: Provide employees with sufficient training to ensure that operators understand the use principles and safety requirements of magnetic lifters.
Operation steps of magnetic lifter
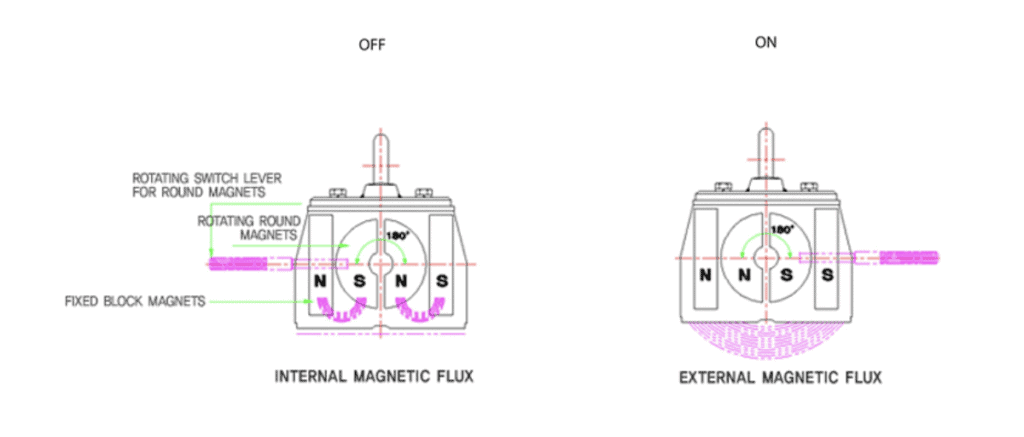
Check the status of the magnetic lifter:
Check the appearance and magnetism of magnetic lifter before use to ensure it is in good working condition.
Select the lifting object:
Make sure the surface of the lifting object is smooth and clean for the best adsorption effect.
Fix the lifter:
Place the adsorption surface of magnetic lifter firmly in the appropriate position of the lifting object to ensure that the magnetism is firmly adsorbed on the surface of the object.
Lifting operation:
Lift the object with the lifter to ensure smooth operation.
Release the lifting object:
After lifting, separate the magnetic lifter from the object by operating the release device.
Maintenance and care of magnetic lifters
Cleaning the magnetic surface:
Regularly clean the dust, oil or iron filings on the magnetic surface to prevent them from affecting the normal function of the magnetic force.
Regular inspection:
Check whether the magnetic force of the lifter has decreased, and confirm whether the magnet is damaged or fatigued.
Storage requirements:
The magnetic lifter should be stored in a dry and cool place to avoid moisture or high temperatures.
Frequently Asked Questions (FAQ)
Q1: Can magnetic lifters be used in high-temperature environments?
A1: Some magnetic lifters are designed to withstand high temperature environments, but you need to choose a dedicated high temperature magnetic lifter based on the use environment.
Q2: Will the magnetic force of a magnetic lifter weaken over time?
A2: Yes, the magnetic force of a magnetic lifter will gradually weaken over time and with frequency of use. Regular inspection and maintenance are key to ensuring that the magnetic force remains stable.
Q3: How do I check the magnetic force of a magnetic lifter?
A3: You can use a dedicated magnetic force tester or conduct an actual lifting test to ensure that the magnetic force can carry the required load.
As an important tool for modern lifting operations, magnetic lifters can significantly improve work efficiency and safety. Choosing a magnetic lifter that suits your needs and performing regular maintenance can ensure its long-term, efficient and stable operation.
- 获取链接
- X
- 电子邮件
- 其他应用
- 获取链接
- X
- 电子邮件
- 其他应用
评论
发表评论